Which is Better DTF or Screen Printing?
The main difference between screen printing and dtf printing is the plate making. Silkscreen printing belongs to the edition printing, need to make the screen version, a color a version, and then repeatedly register color finally made into finished products! Because there is a limit of color, so too many colors, there will be the problem of color inaccuracy, that is, can not do gradient color; production of the screen version is a cost, so the more printed, the average to the cost of each piece of clothing screen version is less, so screen printing is suitable for large quantities, color less orders.
DTF printing, belongs to no plate printing, no need to make plates, through the computer directly print the pattern on the fabric, and then according to the different fabrics to deal with accordingly! Obviously, because no plate making, so a single piece of printing becomes possible; no set of color restrictions, you can print any color and gradient, which provides technical support for private customization, and from the industry point of view, small batch, multi-flower color and short popular cycle has become a consumer trend and concept.
Here we look at these two printing processes and their respective advantages and disadvantages:
DTF printing
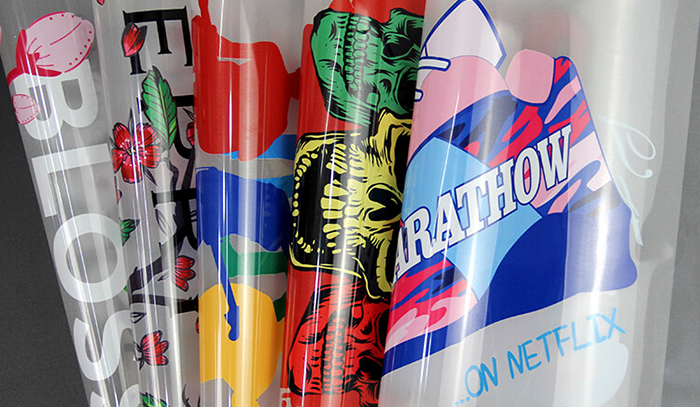
First print the pattern onto the pet film coated with release agent, and after drying, use this film with pattern to iron to the surface of clothes, or other fabrics through high temperature and pressure, leaving the pattern, tear off the waste film, and finish the process of ironing. This hot stamping method, almost suitable for all clothing, all fabrics, provided that the face of different fabrics, have to take different printing process.
Advantages of DTF Transfer Printing
- Good quality. The double layer printing or transfer process ensures that the quality of the print is maintained. In addition, the color fastness is also guaranteed.
- Reliability. Designs are first printed on paper and then on fabric, which makes it easy for us to guarantee the quality of the print. We can check the printing on the paper before printing on the fabric. This guarantee results in fewer printing defects on the fabric.
- No clipping required. No need to cut paper to attach the design to the fabric.
- Easy to operate. Pet film transfer is not a rather complicated process. Its process is really easy to learn. Also, there are no high maintenance requirements, which makes it even more convenient.
- Environmentally friendly technology. Many new contributions are made to make it environmentally friendly. In some cases, the PET used is made in a way that can be recycled.
- Variety of options: When choosing the desired printing technology, the most important area of concern is color limitations. In pet film transfer printing, there is no limit to the number of colors used, making it a better choice.
- Works with all fabrics. PET printing is suitable for all types of fabrics, be it cotton, silk or any other type of cloth. At the same time, DTG is not suitable for all types of fabrics. Generally speaking, PET printing is more suitable for water-based ink and oil-based ink printing.
- Less use of ink. Much less ink is used for printing than other methods. Both white and color inks are used less frequently.
Disadvantages of DTF Printing
- High cost. Cost plays the most important role when investing in any equipment/plant. PET film transfers are expensive compared to direct transfer printers, so economies of scale don’t help reduce their costs either.
- Waste time. While the transfer process helps with assurance, it is still a time-consuming process. It is less efficient for businesses with fewer workers but more demand.
- More waste of resources. Designs are first printed on paper/PET and then transferred to fabric, resulting in more paper/PET waste. These PET papers also cannot be reused, which clearly illustrates the waste of resources.
- Lack of flexibility. Although it is of much higher quality than DTG, it is much less soft and smooth compared to DTG.
If you are looking for top-notch and affordable DTF printers to meet your high-volume printing needs, look no further than Textek DTF Printer. We are a reputable company with unmatched experience in selling high quality DTF printers from popular brands and manufacturers.
Screen Printing
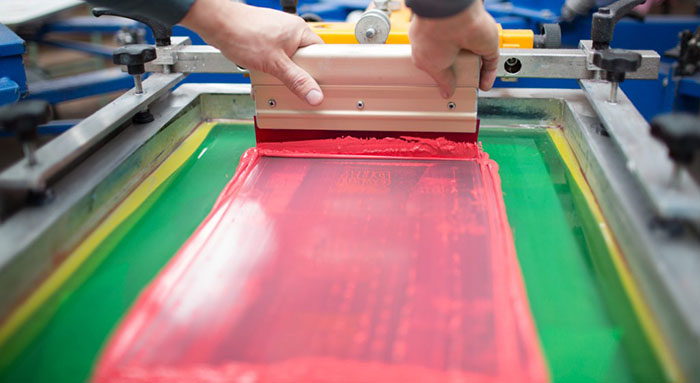
Screen printing refers to the use of a screen as the plate base and the photographic plate making method to make a screen printing plate with graphics. Screen printing consists of five main elements: screen printing plate, squeegee, ink, printing table and substrate. The basic principle of printing is that the graphic part of the screen plate is permeable to ink and the non-graphic part of the screen is not permeable to ink. Printing in one end of the screen printing plate into the ink, with a squeegee on the screen printing plate on the ink part of a certain pressure, while moving at a uniform speed towards the other end of the screen printing plate, the ink in the movement of the squeegee from the graphic part of the screen hole extrusion to the substrate.
Pros and Cons of Screen Printing
Pros:
- More suited for larger single or two color designs.
- Perfect for printing on the cotton and poly cotton clothes.
- Screen printed garments are machine washable as the ink is heat dried.
- The print created by screen printing is bright irrespective of the color of the fabric.
- The print can be ironed.
- Cost effective if printed in bulk.
- There is no limit on the size of the print and it is possible to do all over prints.
Cons:
- Expensive if not printed in bulk.
- As each color is applied separately, the making cost gets higher with each addition of color.
- Separate screens are required for each color.
- Not ideal for multi-colored design.
- Not suitable for coated fabrics.
- The set up and cleaning required after each run is quite time consuming.