Different types of inks in Printing
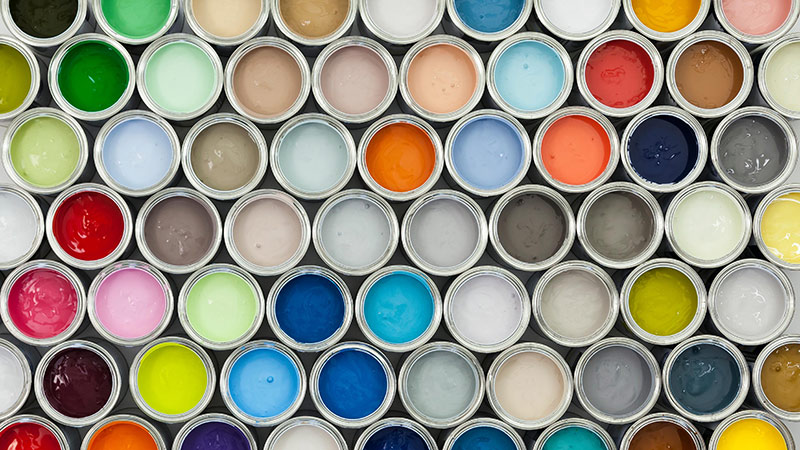
1. Aqueous inks
They are known as aqueous, water-based or self-crosslinking inks, and water is the basis of their composition, to which dyes or pigments have been incorporated. Dyes have very vivid colors and are inexpensive but fade quickly; pigments are more expensive but are more resistant to the passage of time, provided they are preserved under the right circumstances. Photographic quality inks made with pigments maintain colors for a century or more if the print is kept away from sunlight and pollutants.
Aqueous ink printers used for photography can use many colors of inks.
Aqueous inks are non-toxic during the printing process and also afterwards. They are odorless, unlike some solvents. However, to enjoy the best printing quality it is essential to apply a special coating to the surface to facilitate ink absorption and to avoid ink migration when the water has evaporated. This process increases its price when compared to solvent inks or UV inks.
Applications: This type of inks are mainly used for paper and cardboard. Posters, photographs, artwork, point-of-sale advertising, indoor posters and signs, pre-treated canvas, corrugated, materials where the inks cannot be toxic, e.g. food packaging. Most domestic inkjet printers use aqueous inks.
Do not use: These inks are not suitable for outdoor applications, nor for printing on non-absorbent material (although there are foils, plastics and even thin metals that incorporate a special coating for inkjet ink pick-up).
Which printers use this ink? Sheet-fed or roll-fed printers with thermal or piezo-electric printheads.
2. Sublimation inks
These inks are designed to penetrate polyester fabrics or the polyester coating incorporated into solid objects. This ink is printed by piezoelectric printheads on sublimation paper that acts as a temporary ink carrier. The ink is then transferred onto the polyester material by applying heat with a transfer plate. During ironing, the ink is converted into vapor (sublimation) and absorbed by the polyester, forming a permanent bond.
Large rolls of fabric can be printed with sublimation paper using calenders, devices with rollers that reach high temperatures. Smaller garments can be sublimated using transfer plates with a flat plate. There are also transfer plates with specific shapes such as cups or bottles.
It is also possible to print by sublimation directly on the garment, generally made of polyester. In this case, the fabric is placed in the inkjet printer and the ink is applied directly onto the fabric. After printing the image, it must be fixed on a transfer plate or calender, so that sublimation occurs on the fibers of the fabric.
Applications: Used for textiles (garments, signage, banners), as well as flat or slightly curved surfaces that can be coated with polyester and placed on a transfer plate. Examples of these items include phone and computer cases, plates and picture frames made of plastic, wood, glass, metal, ceramic mugs, etc. There are also 3D ovens that allow sublimation on irregular surfaces.
Not to be used: It cannot be used on items that are not made of polyester or do not have the special polyester coating.
Type of printers: inkjet printers with piezoelectric heads.
3. Solvent Inks
These are inks where the dissolution base is a volatile solvent that transports the pigments, and are mainly used for outdoor signage due to their high resistance to sunlight. The result is very durable and they combine perfectly with plastic or paper substrates. The solvent dissolves on the surface of the plastic so that the pigment or incorporated dye is fixed to the substrate after the solvent evaporates. For plastics in general, an approximate outdoor shelf life of five years is indicated.
However, the solvent contains volatile organic substances (VOCs) that generate a very strong odor during the drying process and even for a long time afterwards. For this reason, articles printed with these inks are not suitable for indoors or in confined spaces. It is necessary to wear protective clothing during the printing process.
Applications: outdoor signage and advertising, on vehicles and curtains.
Not for use: indoors, on packaging or non-absorbent substrates.
Type of printers: models with piezoelectric printhead, and generally large format (2 to 5 meters wide).
4. Eco-solvent inks
Eco-solvent inks were developed around the year 2000 as an alternative to the high toxicity and intense odor of solvent inks. They contain fewer hazardous components and do not generate any significant odor during or after printing. Printers with eco-solvent ink can be used in enclosed spaces and offices, because there is no need to ventilate the space. The outdoor life of plastics printed with eco-solvent inks ranges from 18 months to three years, as opposed to five years for solvent inks.
Color intensity is relatively lower, although the quality has improved over successive generations. Some manufacturers have developed eco-solvent metallic and opaque white inks.
The inks dry quickly due to thermal resistance, and the printed items can be handled safely. However, some evaporation occurs within 24 hours. So you will have to wait to laminate the printed surface, otherwise air bubbles will be generated.
Although the prefix “eco” is appealing, it is actually very undefined, because there is no standardization between manufacturers. The inks are not clearly “eco-friendly” and for this reason some manufacturers claim that “eco” refers to “economical”, which is also questionable. Although attempts have been made to develop “eco-friendly” biosolvent inks derived from renewable substances (wheat or soy), they have been unsuccessful due to reduced color strength and low durability.
Although the terminology is somewhat uncertain, there is a third class of solvent inks that are often referred to as “mild solvents.” Offer greater durability than eco inks but still give off some odor and require ventilation.
Applications: for indoor and outdoor signage, billboards, point-of-sale displays, self-adhesive vinyl, polypropylene, vehicle vinyl, etc.
Not to be used: on non-absorbent substrates.
Type of printers: piezoelectric printheads, paper roll driven and also with hybrid configuration from 50cm up to 5 meters.
5. Latex ink or resin ink
This is a hybrid ink composed of water-based, heat-curing resins (polymers) and additives (copolymers) that fix the pigments to the substrate on which it is printed. It has been conceived as an alternative to solvent inks, and offers similar gloss and durability. They are non-toxic, as they do not contain a significant amount of volatile organic compounds (VOCs) and are odorless. This ink is dry when it comes out of the printer and the product can be laminated immediately after printing, eliminating waiting times.
Latex inks are primarily used to decorate walls and create murals.
Although it is called latex ink, it does not contain any latex but is known as such because of its emulsion-like nature.
The print is made on the substrate and a lot of heat is applied from above and below to evaporate the water. The heat also activates the resins in the ink which act to bind the pigments to the substrate and dry to form a tough protective layer against moisture. This application of heat requires high power consumption and limits the type of substrate on which these inks can be applied.
Used for: backlit signage films, photographs, indoor signage, point-of-sale displays, banners, self-adhesive vinyl and polypropylene, wallpaper.
Not to be used: for printing on heat-sensitive materials such as thin vinyl.
Type of printers: thermal or piezo electric printers.
6. UV curing ink
These inks are liquid until exposed to ultraviolet light, at which point they cure and polymerize virtually instantly to form a tough, durable color coating. UV curing also means that the inks are unlikely to cause head clogging.
It is generally rated for a five-year outdoor life, just like solvent inks but with the difference that this ink cures instantly. A liter of UV ink is more expensive than a liter of solvent ink but less of it is used so it is more cost effective.
Early UV inks offered a rather rough and embossed printed surface. However, more recent formulations and current curing techniques have reduced this effect considerably. Some printers allow the final gloss level to be varied to achieve a matte or gloss finish.
UV ink has virtually no volatile organic compounds (VOCs) and is not hazardous when properly cured, but contact with uncured ink can “irritate” the skin and respiratory passages, causing severe allergic reactions. Air extraction and filtration must be ensured at printing locations and in some cases is legally required. UV curing lamps must be properly shielded to avoid radiation to the skin or eyes of operators. Some ozone lamps emit ozone, which is hazardous to health, reinforcing the need for air extraction. Adjusting the wavelength will avoid this effect.
Conventional low-energy lamps generate a negligible amount of ozone. As do the popular LED lamps, which also consume less energy, do not heat up as much and have a longer life than tubes.
Used for: originally used mainly on rigid, non-absorbent substrates such as metal, glass, graphic design on windows, wood, plastics. More flexible formulations have been developed for curtains, banners, nets and flags. There are even more flexible inks for decorating vehicles and for thermoformed plastic containers.
They should not be used for food packaging or garments because of the possibility of uncured ink migration from the substrate and the danger of contact with food or skin. UV inks have a distinctive odor. Conventional metal halide lamps for curing reach very high temperatures, so they do not allow the use of thin heat-sensitive materials, but “cold cure” LED lamps operate at lower temperatures. There are no UV metallic inks, but some systems apply a thin metallic “cold foil” to the ink layer before curing.
Type of printers: only piezo electric printhead printers. Almost all flatbed printers apply UV curing. UV printers are generally coil operated.
7. Solvent-UV hybrid ink
It is an ink that combines a small amount of volatile solvent with a UV-curable resin that holds the pigment in place on a carrier. They are an economical alternative to latex inks because they require less energy to cure and provide better outdoor durability.
The solvent dilutes the liquid polymer to obtain a finer and brighter surface, allowing it to be fixed to the plastic surface. The heat in the flatbed printer evaporates the solvent after printing, locking the ink in place long enough to reach the UV lamp for final curing.
The finish appears to be a highly colorful and glossy print with high durability. In addition, it does not release solvents, so it can be laminated immediately.
It is used for: roller printing of indoor and outdoor signage, self-adhesive vinyl.
They should not be used for: food packaging and printed garments.
Printer type: Piezo heads designed for this type of ink.
8. Solid ink
At room temperature, this ink has a solid waxy texture that turns into a liquid gel in the print head when heated. An ink jet deposits it on a cold holder and the ink immediately solidifies.
The process can be used to print on inexpensive paper, textiles and garments that do not contain any special coatings, as well as on many non-absorbent materials such as plastics and wood. The colors are very bright and consistent because they do not require any type of absorption. However, some inks seem to be poorly resistant to rubbing.
It is used for: large format posters, CAD/GIS plans, point-of-sale signs, signs on waterproof stands.
It should not be used for: prints for viewing in the foreground (e.g. for art or photography), long-life supports, banners, textiles.
Printer type: Dedicated thermal head.